Daheda DHTLHR-400 metal chip deoiler (Iron slag oil remover, aluminum chip oil remover, copper slag oil remover, industrial oil remover, 1400 rpm cutting fluid oil slinger. The industrial oil remover is a new product designed and manufactured by our company based on similar foreign products and in combination with domestic actual conditions. This product is mainly used for dehydration and oil removal of various parts. The equipment is manufactured according to the technical data of the Japanese Tanaka Technical Research Institute oil remover, and two major improvements are made on the basis of the original machine in Japan. It is applicable to The rapid degreasing of metal cutting chips has been successfully used in domestic and Japanese wholly-owned enterprises, such as Kebao Electric (Jiaxing), Shinon Motor (Dongguan), and Matsushita Electric (Wuxi) Co., Ltd. Luode Precision Machinery (Wuxi) Co., Ltd. Jiaye Precision Hardware (Wuxi) Co., Ltd. has received favorable reviews from hundreds of enterprises.
Working principle of Daheda metal cutting chip high-speed deoiling machine, industrial deoiling machine, 1400 rpm cutting fluid oil slinger
During the operation of the degreaser, the centrifugal rate is used to throw oil towards the periphery of the outer wall and the top above. These two parts are the parts for collecting oil. In addition, there are tens of vertical grooves arranged uniformly on the inner wall of the degreaser, which can allow the liquid to flow smoothly. Especially when small objects are encountered, the residue on the inner wall of the metal wire forms a vacuum space outside, fully removing the oil.
Main mechanisms of Daheda metal cutting chip high-speed deoiler, industrial deoiler, 1400 rpm cutting fluid oil slinger:
1. Maintain a 1-degree inclination and use centrifugal force to make the liquid flow upward.
2. Between these two parts, there are 8-10 small holes of 3-4 mm in the inner wall.
3. Metal filings are isolated from finely powdered materials to improve the oil removal rate.
4. The outer wall does not need to have many holes, and the solid oil removal rate in the middle naturally increases.
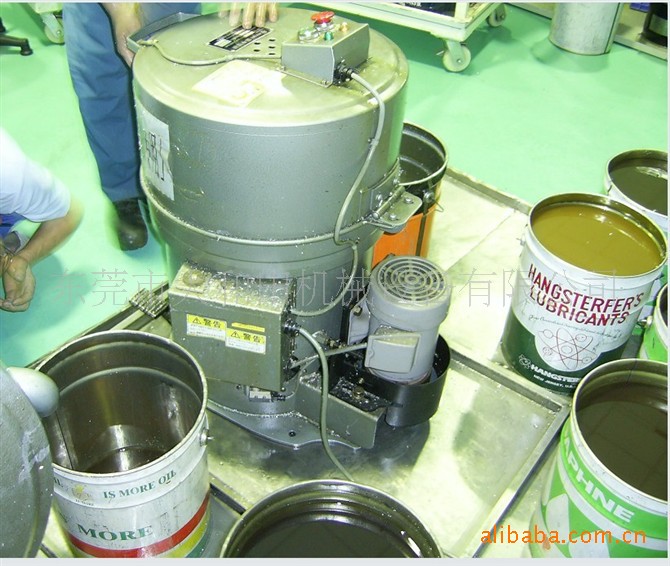
Daheda Metal Cutting Chip High Speed Oil Remover, Industrial Oil Remover, 1400 RPM Cutting Fluid Oil Thrower Features:
1. The deoiler has an ideal state for deoiling.
A. Lightweight design, easy to use.
The oil outlet groove is composed of dozens of 3-4 mm holes in the upper part, and there are no holes in other parts of the outer wall. Although the surrounding area is thin, it is very strong.
C. Don't worry about the oil spilling out from the upper edge groove. There are also several grooves on the four walls of the machine.
The tapered design of the outer circumference makes it easy to remove curly cutting debris.
2. A standard timing switch allows for controlled deoiling.
3. The design of putting in and taking out the barrels of the degreaser is more convenient.
4. The 1400 rpm high-speed design, balanced rotation, and special bearing structure can reduce vibration.
5. When items are unbalanced, simply adjust the front and rear of the bucket to eliminate the vibration.
6. When it is difficult to install, you can constantly move the location or install auxiliary facilities for use.
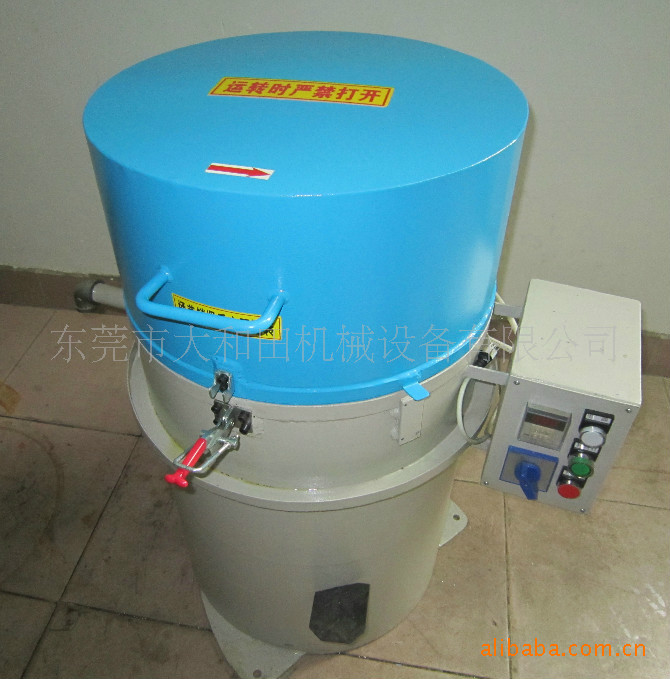
Main technical data of Daheda metal cutting chip high-speed deoiler, industrial deoiler, and 1400 rpm cutting fluid deoiler:
Model: DHTLHR-400
Rotary drum size: 300 × 370MM
Rotary cylinder volume: 0.028m3
Operating speed: 1400 rpm
Working voltage: 380V
Motor power: 1.1KW
Processing capacity: 26KG/time
Oil removal time: 2-3 minutes/time
Shockproof structure clutch
Overall dimension: 800 × 850MM
Operating Weight: 148KG
Use of Daheda Metal Cutting Chip High Speed Oil Remover, Industrial Oil Remover, 1400 RPM Cutting Fluid Oil Thrower:
Before using this degreaser, it is necessary to first check whether the electrical components of each component are damaged or have leakage faults due to transportation, and whether the mechanical operating part is flexible. Then, select a suitable location (it should be installed in a ventilated and dry place as much as possible), level the machine, tighten the anchor bolts, and connect the power supply for a 30 minute test run, To check the rotation direction of the rotary drum and the working condition of each component (when viewed from one side down, the normal rotation direction is counterclockwise), and when everything is normal, it can be delivered for use.
When loading and unloading workpieces, it is necessary to stop the machine and be careful not to overload the rotating drum or suffer violent impact. After installing the parts, the cover must be closed before starting the motor to ensure safe production and extend the working life of the machine. The oil removal time can be flexibly controlled based on the actual situation of the dried parts. After the work is completed, the main power supply must be disconnected to avoid accidents.
The operation and maintenance of the degreaser should be carried out by full-time personnel who are familiar with the situation, and the machine should be regularly inspected and lubricated (1-2 weeks). When the weight of the dried workpiece becomes large and loses stability, the motor should be intermittently started to maintain the balance of the rotating drum before operation. It should be avoided that unnecessary damage caused by operations that violate the operating procedures, so that the degreaser can achieve the maximum efficiency and achieve the maximum effect. (Note: When starting the rotary drum, you can first rotate the motor and repeat it several times before entering normal operation to ensure that the parts in the rotary drum become uniform.)